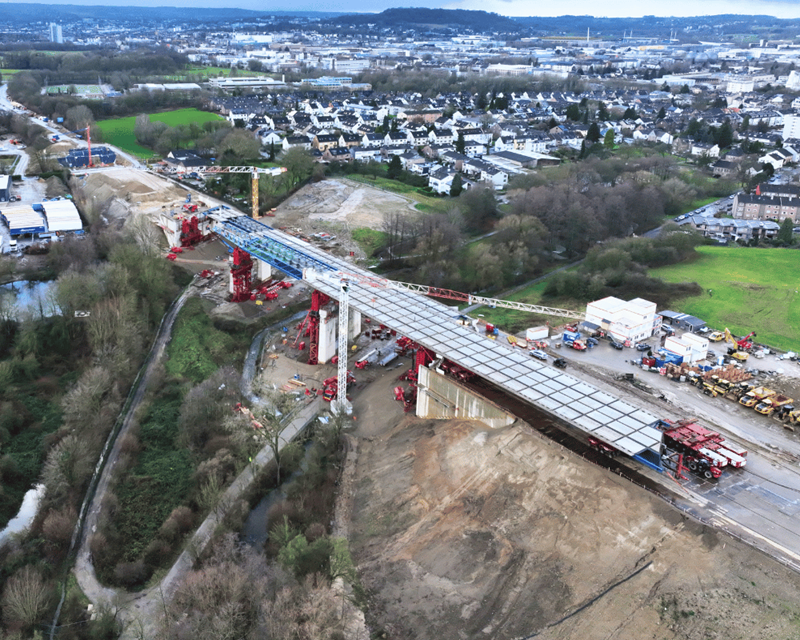
Sector:
Case study
Civil Engineering
Expertise:
Skidding
Heavy transport
Heavy lifting
Benefits:
Optimized schedule
Reduced disruption
Increased safety
Reduced preparation
Location:
Germany
The complex installation was achieved by skidding the bridge across elevated jacking towers
Mammoet are specialists in Accelerated Bridge Construction (ABC), possessing the engineering knowledge and equipment to allow bridges to be built closer to installation sites and assembled in larger, and therefore fewer, pieces – saving considerable time and cost.
The Haarbachtal bridge crosses the Haarbach valley on the A544 highway, near Aachen. It dates from the 1950s and is a key bridge in Germany, connecting Aachen to Cologne.
Over time, the original structure, built in 1956, suffered damage in several places, initially limiting traffic to one lane in each direction and eventually requiring the structure to be replaced. This required a full closure of the bridge and innovative approaches to shorten the construction time and get traffic flowing again as quickly as possible.
Mammoet was asked by AMAND Bau NRW to help launch the new steel composite bridge, which comprised two structures measuring 160m and weighing 1,340t.
The project posed significant engineering challenges. Height was a factor, and the bridge needed to be launched at a downward 2% angle. Its new abutments and pillars were also positioned at a 30-degree angle.
Considerable planning and engineering were required to achieve this complex bridge launch safely and to schedule. Its structures would need to be skidded over jacking towers built onto taller supports for greater height and stability.
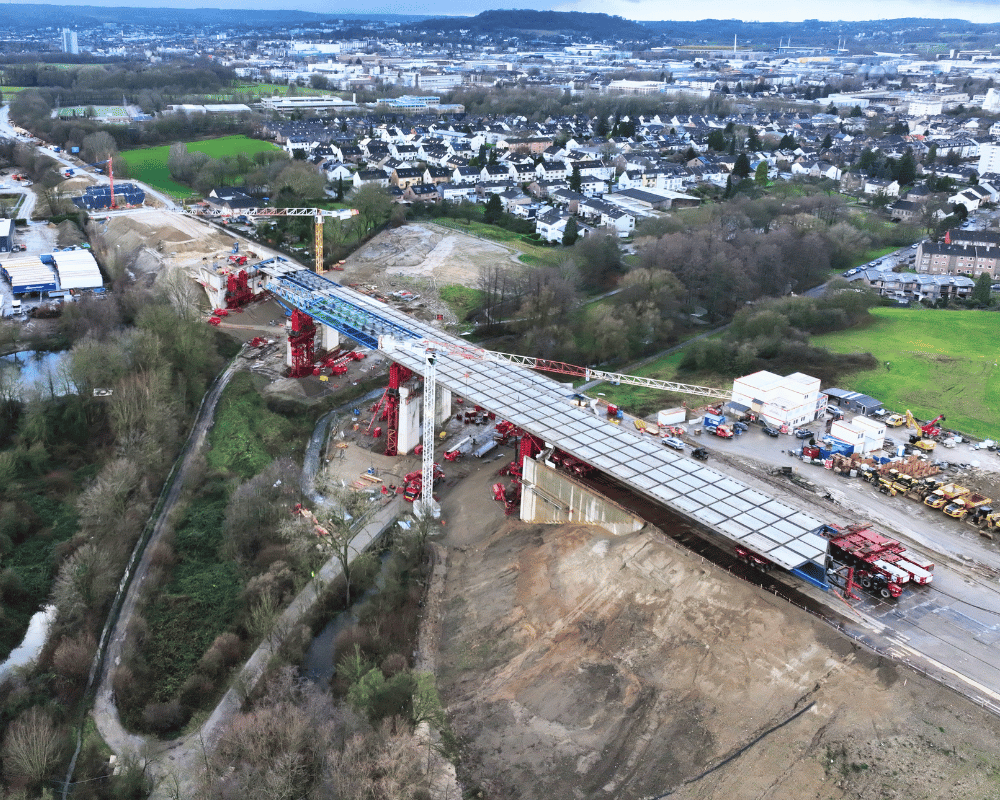
Skidding over jacks
The old bridge was rapidly dismantled using controlled explosives in January 2024. The two new substructures were constructed on site and their installation began in December that year.
Mammoet’s scope was to transport the new bridge structures from their build location and position them over, and then onto, their newly fabricated pillars and abutments.
Mammoet Self-Propelled Modular Transporters (SPMTs) were used to lift and drive the structures to the launch position near the first abutment on the east side of the bridge.
For this step, 68 axle lines of SPMT were used, configured in four groups of trailers set up in six hydraulic groups. The front and back groups were put to a constant pressure, while the four in the middle prevented the bridge from deflecting excessively.
Before this, Mammoet assembled a complex jacking system to gradually lower each structure onto its foundations. It involved two different systems working in tandem, elevated on supports.
The jacking system could not be used on the pillars as the bridge structures needed to be set down on them. Therefore, temporary towers were erected beside the two pillars and abutments. On these sat Mammoet’s Mega Jack 800 system (two bases per tower) coupled with ‘correction’ jacks (500t and 800t) fitted with launching plates equipped with Teflon pads.
“The height of the Mega Jack system was around 25 meters, which is quite high and would not be self-stable with the acting launching forces at the top,” explains Koen Harthoorn, Lead Engineer at Mammoet. “Therefore, the temporary towers were connected horizontally to the pillars and the abutments to achieve greater stability.
The Mega Jack system was finally stabilized with strand jacks and fixed bracings connected to the abutments. Because everything needed to be arranged at a 30-degree angle, it meant the forces would act in directions you wouldn’t normally expect. Taking that into account was an additional challenge.”
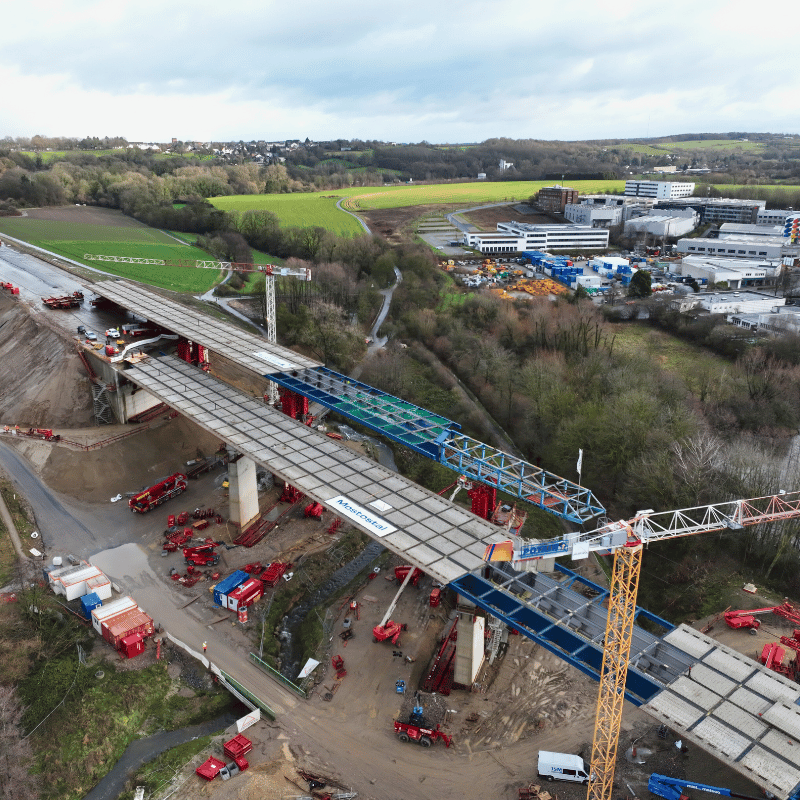
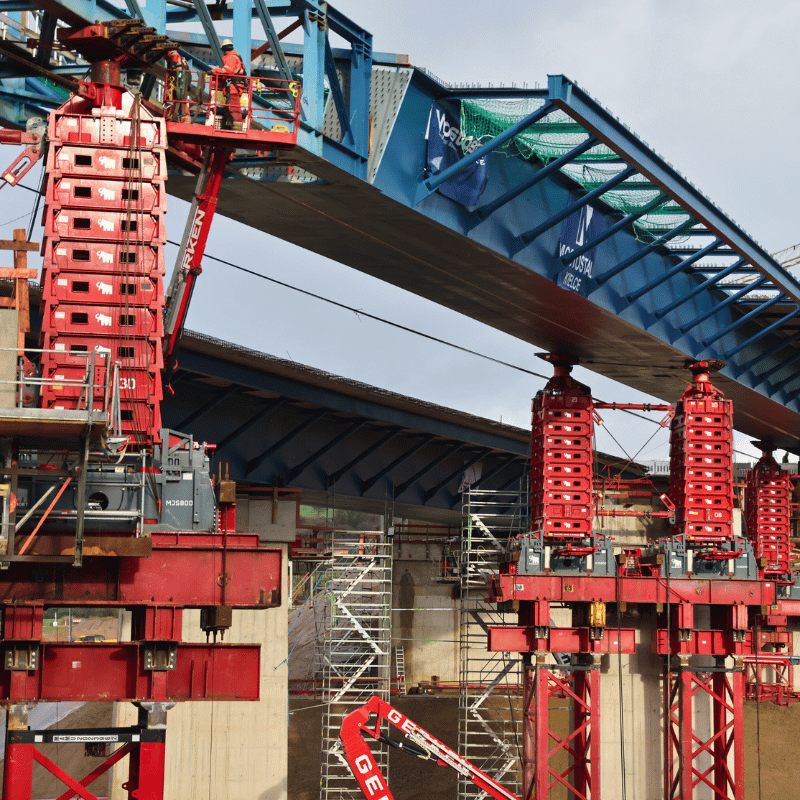
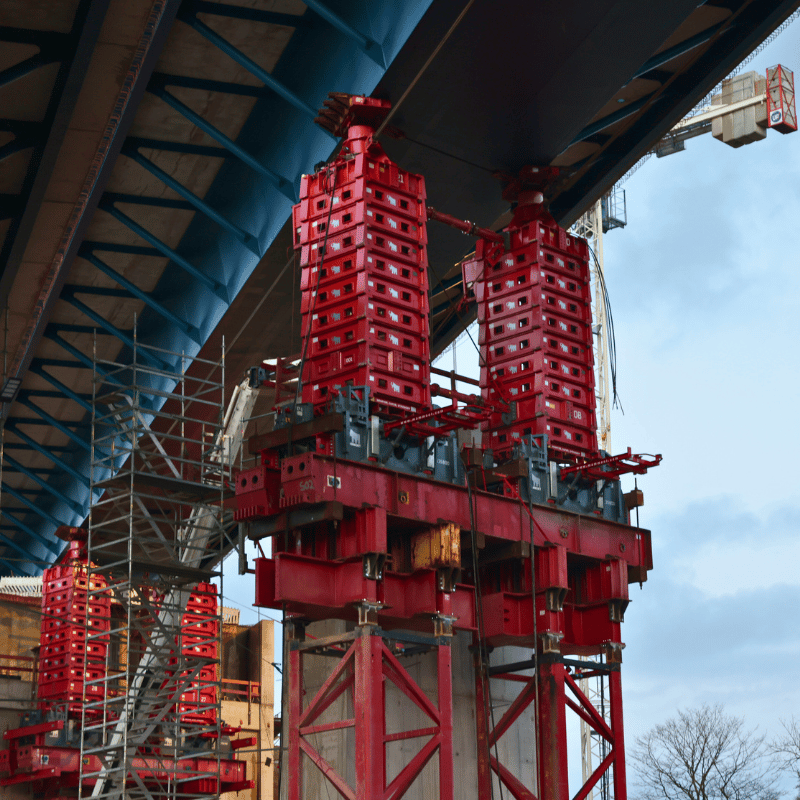
Launching at angles
The bridge structures were fitted with a ‘Vorbauschnabel’ – a temporary nose section to help them land comfortably onto the next launching plate. This increased their length to 190m and weight to 1,413t.
During the launch, each SPMT group was gradually removed as it reached the edge of the first abutment. This continued until the remaining SPMTs no longer had any traction and the process was taken over by hydraulic stand jacks. Because of the two-degree slope, winches were used to act as breaks if needed.
The bridge was lowered with the Mega Jack 800 system on all four towers. At a particular stage, it was lowered on three towers, while on the fourth tower only a ‘correction’ jack was used. The ‘correction’ jacks also helped to level the bridge. Combining these two methods at the same time was a unique approach.
With the jacking towers taking three weeks to construct, the team suggested installing skid tracks between the east and west pillars and abutments. This meant the towers could be moved to the adjacent sets with minimal effort and reused when installing the second bridge structure.
Thanks to careful planning and innovative time-saving methods, construction was achieved in just 22 months, with each substructure taking one and a half days to install. This was accomplished during adverse weather conditions and on a busy site with groundwork taking place.
Enabling the bridge to be fabricated on-site was also an advantage. It could be constructed at normal working height, allowing the project to be carried out safely and more efficiently.